安徽汽车压力传感器生产工艺的关键步骤及技术要点如下:
1. 材料选择与预处理
采用高纯度单晶硅片作为材料,通过氧化、光刻、离子注入等半导体工艺制备压敏电阻层。金属壳体选用304不锈钢或钛合金,经精密数控机床加工后,采用超声波清洗和等离子体活化处理,确保表面洁净度和结合性能。高分子密封材料需进行预烘烤除湿处理,降低热膨胀系数差异。
2. MEMS微加工工艺
通过深反应离子刻蚀(DRIE)在硅基底形成微米级膜片结构,控制膜片厚度精度达±0.5μm。采用磁控溅射技术沉积氮化硅绝缘层,厚度控制在200-500nm。电阻桥路通过离子注入掺杂形成,方阻值控制在1-5kΩ/□,温度系数匹配精度优于0.05%/℃。
3. 芯片封装工艺
采用倒装焊技术实现芯片与陶瓷基板互联,焊点间距≤100μm。玻璃-金属密封工艺在850℃氮气环境中进行,漏率<1×10^-8 mbar·L/s。灌封工序使用双组分环氧树脂,真空脱泡处理后进行梯度固化,固化收缩率控制在0.2%以内。
4. 温度补偿校准
在-40℃至150℃温区内进行三点温度补偿,采用激光修调技术调整补偿电阻,使温度漂移系数≤±0.5%FS/100℃。压力标定使用0.05级标准压力源,全量程线性度校准达±0.1%FS。老化测试包含100万次压力循环和2000小时高温高湿试验。
5. 智能制造控制
应用机器视觉进行焊点质量检测,缺陷识别率≥99.7%。装配过程采用六轴机械手,重复定位精度±5μm。数据追溯系统记录每个传感器的200+工艺参数,实现全生命周期质量。产线配备在线SPC系统,关键参数CPK值≥1.67。
安徽地区依托合肥工业大学等科研机构,在MEMS传感器领域已形成完整产业链,本地化配套率达75%以上。采用自动化率90%以上的智能产线,产品通过IATF 16949认证,年产能突破5000万只,配套国内主流新能源车型。
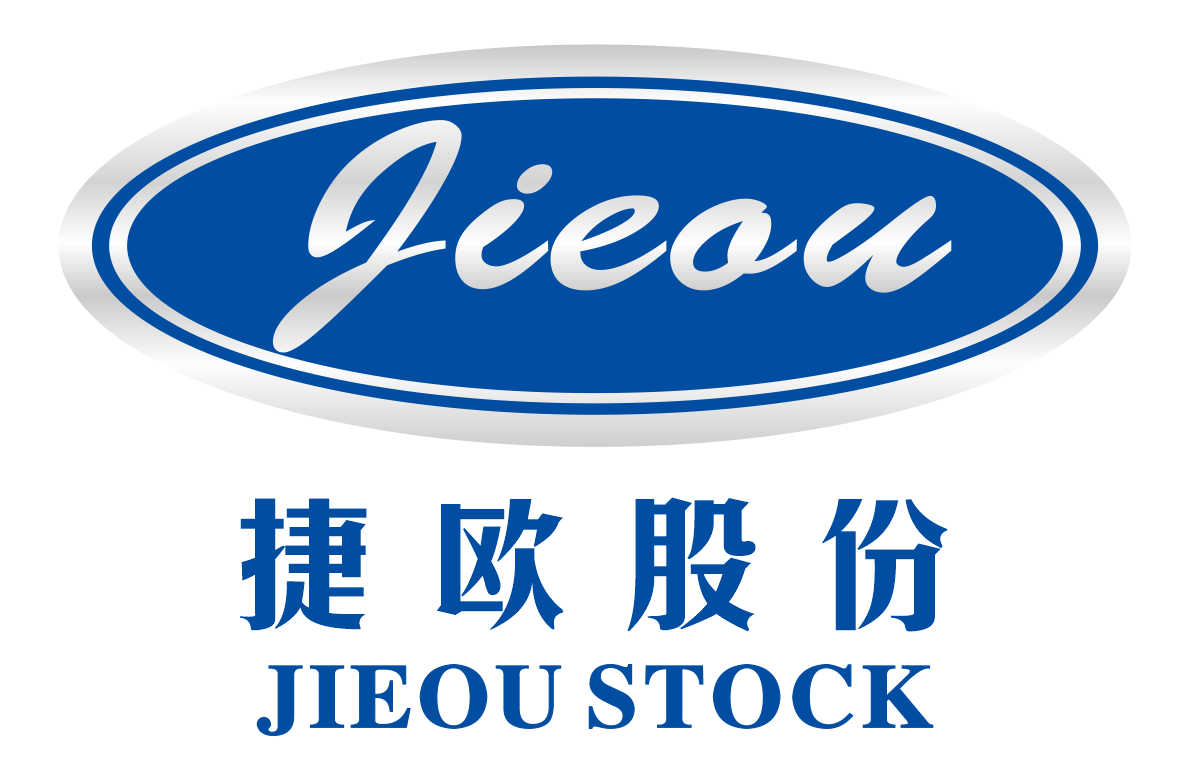